The Downspouts Roll Forming Machine: An Indispensable Asset in Rainwater Management.In the world of construction and building maintenance, downspouts play a crucial role in efficiently channeling rainwater away from roofs and structures, safeguarding them from potential water damage. At the heart of their production lies the remarkable downspouts roll forming machine, a technological marvel that has transformed the way these essential components are manufactured.
I. The Working Principle
The downspouts roll forming machine operates on a precise and continuous process. It all begins with the selection of a suitable raw material, typically aluminum or steel in the form of coils. These coils are loaded onto the machine’s decoiler, which serves as the starting point of the production line. The decoiler ensures a smooth and controlled release of the metal strip, maintaining an appropriate tension to prevent any irregularities during the subsequent forming steps.
As the metal strip leaves the decoiler, it enters the forming section of the machine. Here, it encounters a series of carefully designed and precisely positioned forming rollers. These rollers are custom-engineered to gradually shape the initially flat strip into the specific profile of a downspout. Each roller has its own unique contour and function, working in harmony to bend, curve, and mold the metal in a step-by-step manner. For instance, the initial rollers might start by creating a basic cylindrical shape, while the following ones refine the edges, add flanges if necessary, and ensure the overall structural integrity of the downspout.
Once the downspout has been fully formed to its desired shape, it proceeds to the cutting stage. The cutting mechanism, which can be equipped with advanced servo-motor technology for high precision, slices the continuous length of the downspout into individual sections of the required length. This length can be easily adjusted according to specific project requirements, allowing for flexibility in production.
II. Key Components and Their Functions
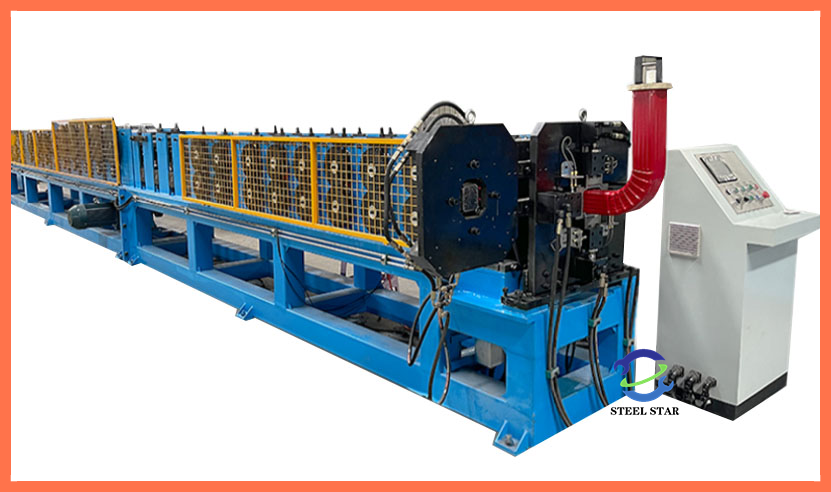
- The Decoiler: This component is vital for the smooth operation of the entire machine. It not only holds the coil of raw material but also incorporates tension control systems. In a busy manufacturing facility producing downspouts for numerous building projects, proper tension management by the decoiler is essential. If the tension is too loose, the metal strip may wrinkle or buckle during forming, resulting in defective downspouts. On the other hand, excessive tension could lead to stretching or even breakage of the material.
- Forming Rollers: These are the core elements of the machine, responsible for the actual transformation of the metal strip. Made from durable and high-quality materials, they are designed with meticulous precision. Different types of downspouts, whether round, square, or rectangular, require specific sets of forming rollers. The rollers’ surfaces are carefully crafted to exert the right amount of pressure at the right points to ensure consistent and accurate shaping. For example, when manufacturing a square downspout, the rollers need to create sharp corners and straight sides with utmost precision.
- Cutting Device: The cutting device is what turns the continuous stream of formed downspouts into manageable, individual units. Its accuracy is of utmost importance. In large-scale construction projects where multiple downspouts need to be installed in a coordinated manner, even a slight variation in the cut length could lead to installation difficulties. Advanced cutting devices can achieve extremely tight tolerances, ensuring that each downspout fits perfectly into the overall rainwater drainage system.
- Control Panel: Acting as the nerve center of the machine, the control panel allows operators to have full control over the production process. They can adjust parameters such as the speed of the rollers, the pressure applied during forming, and the length at which the downspouts are cut. This flexibility enables the machine to adapt to various production requirements, whether it’s producing a small batch of custom-designed downspouts for a heritage building or a large quantity of standard ones for a new housing development.
III. Advantages in Manufacturing
- Efficiency and Productivity: The downspouts roll forming machine is a powerhouse when it comes to production speed. It can churn out a significant number of downspouts in a short amount of time, far outpacing traditional manufacturing methods that involve manual cutting and shaping. This increased efficiency is a boon for manufacturers catering to the demands of large construction projects, ensuring that the required downspouts are delivered promptly.
- Cost-Effectiveness: By automating the production process, labor costs are significantly reduced. Fewer workers are needed to oversee the manufacturing of downspouts, as the machine takes care of the complex forming and cutting operations. Moreover, the precise control over material usage minimizes waste. The forming rollers ensure that the metal is utilized optimally, reducing scrap and maximizing the yield from each coil of raw material, thereby lowering overall production costs.
- Quality and Consistency: Every downspout produced by this machine adheres to the same high standards of quality and dimensional accuracy. The uniformity in shape, size, and structure ensures seamless integration when installing the downspouts into a building’s rainwater drainage system. This consistency not only enhances the performance of the downwater management system but also reduces the likelihood of leaks or other water-related issues in the long run.
IV. Applications in the Construction Industry
Downspouts fabricated by these roll forming machines are ubiquitous in the construction world. In residential buildings, they are essential for directing rainwater from the roof gutters safely to the ground, preventing water from pooling around the foundation and causing damage such as cracks or mold growth. Different styles and sizes of downspouts can be chosen to match the aesthetic and functional requirements of the home, whether it’s a modern minimalist design or a traditional cottage-style house.
In commercial and industrial structures, downspouts are even more critical due to the larger roof areas and higher volumes of rainwater runoff. They are often designed to handle heavy flows of water and are made from more durable materials. For example, in a large office building or a manufacturing plant, downspouts with larger diameters and sturdier construction are employed to ensure efficient drainage and protect the building from potential flooding.
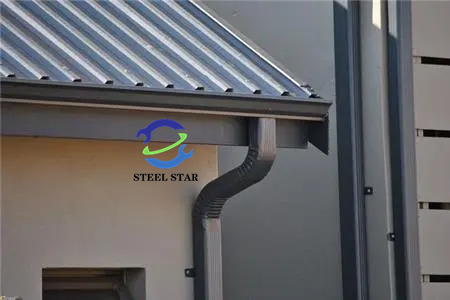
V. Innovations and Future Trends
The field of downspouts roll forming machines is constantly evolving. One notable trend is the integration of intelligent control systems. These systems can monitor the production process in real-time, automatically adjusting parameters such as roller speed and cutting length based on sensor feedback. This not only further improves the quality of the downspouts but also reduces the occurrence of errors and downtime.
Another exciting development is the exploration of new materials. Manufacturers are increasingly looking at using recycled materials or composite alloys that offer enhanced corrosion resistance and durability while maintaining the necessary structural properties. Additionally, there is a growing emphasis on designing downspouts with improved aesthetics, such as those with decorative finishes or unique shapes, to better blend with modern and sustainable building designs.
In conclusion, the downspouts roll forming machine is a cornerstone of the rainwater management manufacturing process. Its ability to produce high-quality, efficient, and customizable downspouts makes it an invaluable tool for the construction industry. As technology continues to advance, we can expect these machines to continue evolving, providing even more innovative solutions for building a more sustainable and water-resistant built environment.
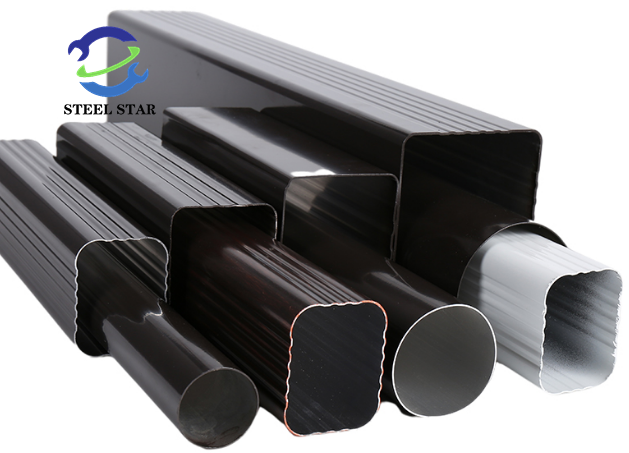
Website:
www.greatforming.com (English)
www.arabicgreatforming.com (عربي)
www.russiangreatforming.com(Русский)
www.spanishgreatforming.com(Español)
www.frenchgreatforming.com(Français)
www.portuguesegreatforming.com(Portuguese)
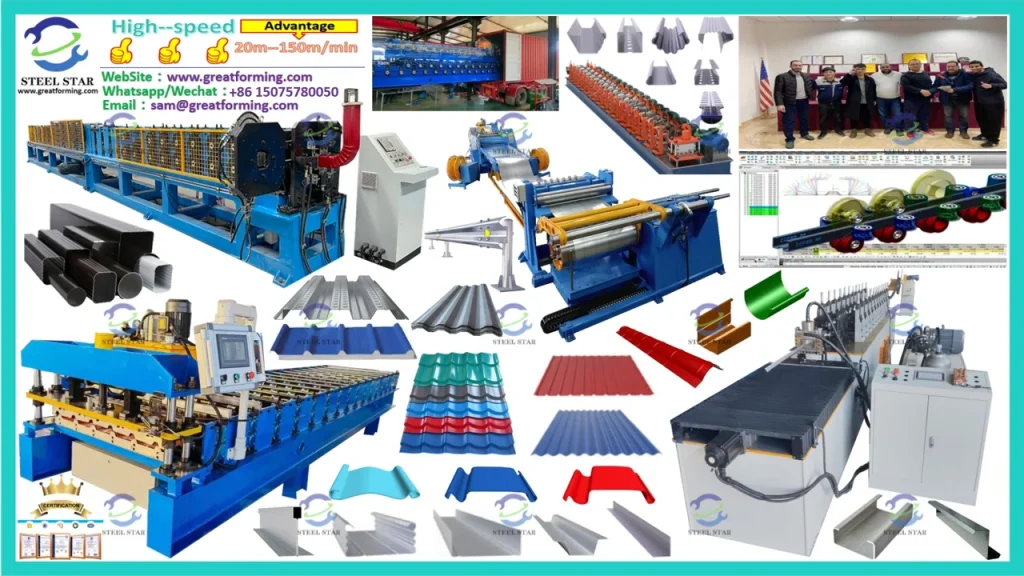