Bending Equipment and Bending Machines: Shaping the World of Metal Fabrication
Abstract: Bending equipment and bending machines play a crucial role in the metal fabrication industry. This article delves into the various types, working principles, applications, technological advancements, and considerations related to these essential tools. It explores how they have revolutionized the way metals are shaped and formed, enabling the creation of complex and precise structures in diverse fields.
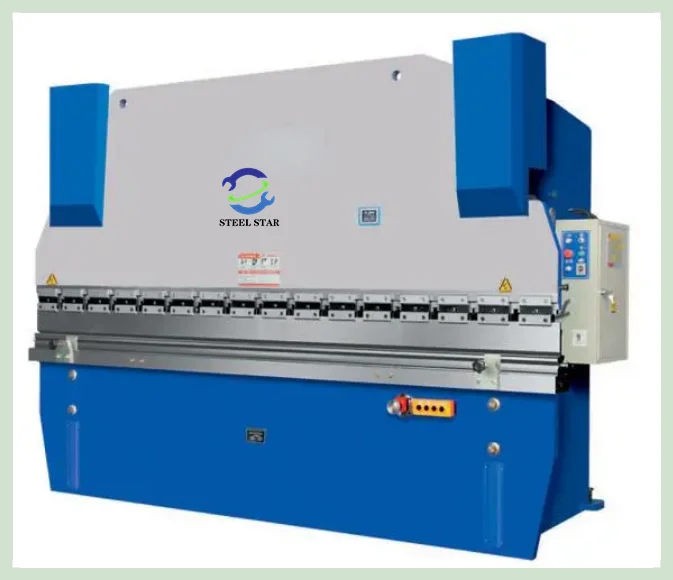
1. Introduction
In the realm of metalworking, the ability to bend and shape metal sheets and profiles is fundamental. Bending equipment and bending machines have emerged as the workhorses of this process, allowing manufacturers to transform flat metal into a myriad of three-dimensional forms. From simple angles to intricate curves, these machines have the power to bring designs to life and meet the demands of various industries.
2. Types of Bending Equipment and Machines
2.1 Press Brakes
Press brakes are perhaps the most well-known type of bending machine. They consist of a bed, a ram, and a tooling system. The metal workpiece is placed on the bed, and the ram, which is actuated by hydraulic, mechanical, or servo-electric power, forces the upper tool (punch) against the lower tool (die) to create the desired bend. Press brakes are highly versatile and can handle a wide range of metal thicknesses and lengths. They are commonly used in the fabrication of sheet metal parts for industries such as automotive, aerospace, and construction. For example, they can produce the brackets, frames, and enclosures that are essential components in these sectors.
2.2 Roll Benders
Roll benders are designed to bend metal tubes, pipes, and bars. They work by passing the workpiece through a set of rollers that gradually apply pressure and curve the material. Roll benders are available in different configurations, including three-roll and four-roll designs. Three-roll benders are often used for simple bends, while four-roll benders offer more flexibility in creating complex curvatures. These machines are widely utilized in the manufacturing of furniture, handrails, and structural steel components. In the furniture industry, roll benders can shape the legs and frames of chairs and tables, adding an aesthetic and functional element to the final product.
2.3 Tube Bending Machines
Specifically engineered for bending tubes, tube bending machines come in various forms. There are mandrel benders, which use a mandrel to support the inside of the tube during bending, preventing it from collapsing or wrinkling. This is crucial when working with thin-walled tubes or when tight radii bends are required. Another type is the rotary draw bender, which rotates the tube while pulling it around a bending die. Tube bending machines are indispensable in industries like plumbing, HVAC (heating, ventilation, and air conditioning), and the manufacturing of bicycles and motorcycles. For instance, in the automotive exhaust system manufacturing, tube bending machines are used to create the complex tubing configurations that optimize the flow of exhaust gases.
2.4 Plate Bending Rolls
Plate bending rolls are used to bend metal plates into cylindrical or conical shapes. They consist of three rolls – a top roll and two bottom rolls. The plate is fed between the rolls, and by adjusting the position and rotation of the rolls, the desired curvature is achieved. These machines are essential in the production of pressure vessels, tanks, and large-diameter pipes. In the oil and gas industry, plate bending rolls are used to fabricate storage tanks and pipeline components that can withstand high pressures and harsh environmental conditions.
3. Working Principles
3.1 Hydraulic Systems
Many bending machines, especially large press brakes, utilize hydraulic systems. The hydraulic power unit generates high-pressure fluid that is transmitted to cylinders. These cylinders actuate the ram or other moving parts of the machine. The advantage of hydraulic systems is their ability to provide a large amount of force, making them suitable for bending thick and hard metals. The force can be precisely controlled by adjusting the pressure of the hydraulic fluid, allowing for accurate and repeatable bending operations.
3.2 Mechanical Drives
Mechanical drive bending machines, such as some smaller press brakes and roll benders, rely on gears, levers, and screws to transmit power and motion. Mechanical drives are known for their simplicity and reliability. They offer a cost-effective solution for less demanding bending tasks. For example, in a small workshop that mainly produces simple sheet metal brackets, a mechanically driven press brake can efficiently perform the required bends with minimal maintenance requirements.
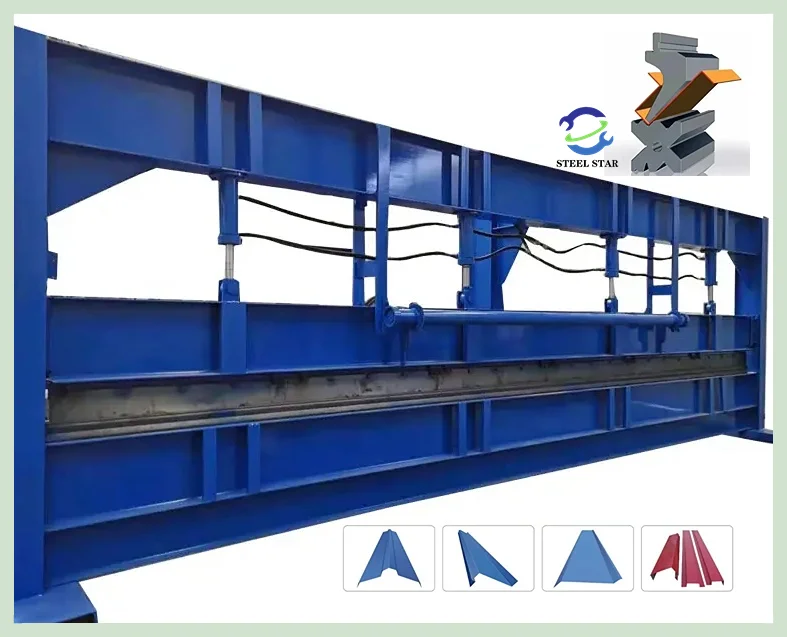
4. Applications in Different Industries
4.1 Automotive Industry
In the automotive sector, bending equipment is used extensively. Press brakes are used to fabricate body panels, chassis components, and brackets. Tube bending machines create the fuel lines, brake lines, and exhaust systems. The precision and reliability of these machines are crucial in ensuring the safety and performance of automobiles. For example, the accurate bending of the chassis components contributes to the vehicle’s structural integrity and handling characteristics.
4.2 Aerospace Industry
The aerospace industry demands the highest levels of precision and quality. Bending machines are used to manufacture aircraft wings, fuselage frames, and engine components. The materials used in aerospace, such as aluminum alloys and titanium, are often difficult to work with due to their high strength and low ductility. Specialized bending equipment with advanced tooling and control systems is required to achieve the tight tolerances and complex geometries needed. For instance, the bending of wing spars must be extremely precise to ensure proper aerodynamic performance and structural strength.
4.3 Construction Industry
In construction, bending machines are used to produce structural steel elements such as beams, columns, and trusses. Plate bending rolls are used to create curved roofing and cladding panels. The ability to fabricate custom-shaped metal components on-site or in a fabrication shop allows for more creative and efficient building designs. For example, the use of curved steel beams can enhance the aesthetic appeal of a building while also providing structural support.
4.4 Furniture and Interior Design
The furniture and interior design industries rely on bending machines to create unique and stylish pieces. Roll benders can shape the legs and frames of furniture, while press brakes are used to fabricate decorative panels and enclosures. Tube bending machines can produce handrails, curtain rods, and other decorative metal elements. The versatility of bending equipment enables designers to experiment with different shapes and forms, adding a touch of elegance and functionality to interior spaces.
5. Technological Advancements
5.1 CNC Control Systems
Computer Numerical Control (CNC) systems have revolutionized bending machines. With CNC, operators can program the machine to perform complex bending sequences automatically. The CNC controller precisely controls the movement of the tools, the bending angle, and the speed of operation. This not only improves the accuracy and repeatability of the bending process but also allows for rapid changeovers between different jobs. For example, a CNC press brake can be programmed to produce a variety of sheet metal parts with different bending angles and lengths in a single production run.
5.2 3D Bending Simulation Software
To further enhance the precision and efficiency of bending operations, 3D bending simulation software has been developed. This software allows designers and engineers to simulate the bending process before it is actually performed on the machine. They can input the material properties, the dimensions of the workpiece, and the desired bending parameters, and the software will predict the outcome, including any potential issues such as springback or tool interference. This helps to optimize the tooling design and the bending process, reducing errors and waste.
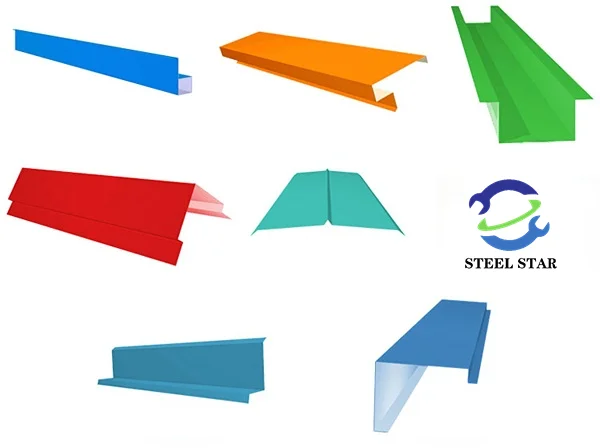
5.3 High-Strength Tooling Materials
As the demand for bending harder and thicker metals has increased, the development of high-strength tooling materials has become essential. Advanced tool steels and carbide inserts are now used in bending machines. These materials can withstand the high forces and wear associated with bending tough alloys, increasing the tool life and reducing the need for frequent tool changes. This not only improves the productivity of the bending process but also helps to maintain the accuracy of the bends over time.
6. Considerations in Selecting and Using Bending Equipment
6.1 Material Compatibility
Different metals have different mechanical properties, such as hardness, ductility, and yield strength. When selecting a bending machine, it is crucial to consider the type of material that will be processed. For example, a machine that is suitable for bending mild steel may not be able to handle the same thickness of stainless steel or aluminum due to their different bending characteristics. Understanding the material compatibility helps to ensure proper bending results and avoid damage to the machine and the workpiece.
6.2 Bending Capacity and Precision Requirements
The required bending capacity, including the maximum thickness and length of the workpiece, must be determined. Additionally, the precision requirements of the final product, such as the allowable tolerance for the bending angle, must be considered. A machine with insufficient bending capacity will not be able to handle the job, while a machine that lacks the necessary precision may result in defective parts. Matching the machine’s capabilities to the specific job requirements is essential for successful metal fabrication.
6.3 Safety Features
Bending machines are powerful tools that can pose significant safety risks if not properly used. Safety features such as emergency stop buttons, safety guards, and interlocks should be present. Operators should be trained in safe operating procedures and wear appropriate personal protective equipment. Regular safety inspections and maintenance of the machine are also necessary to ensure a safe working environment.
Website:
www.greatforming.com (English)
www.arabicgreatforming.com (عربي)
www.russiangreatforming.com(Русский)
www.spanishgreatforming.com(Español)
www.frenchgreatforming.com(Français)
www.portuguesegreatforming.com(Portuguese)
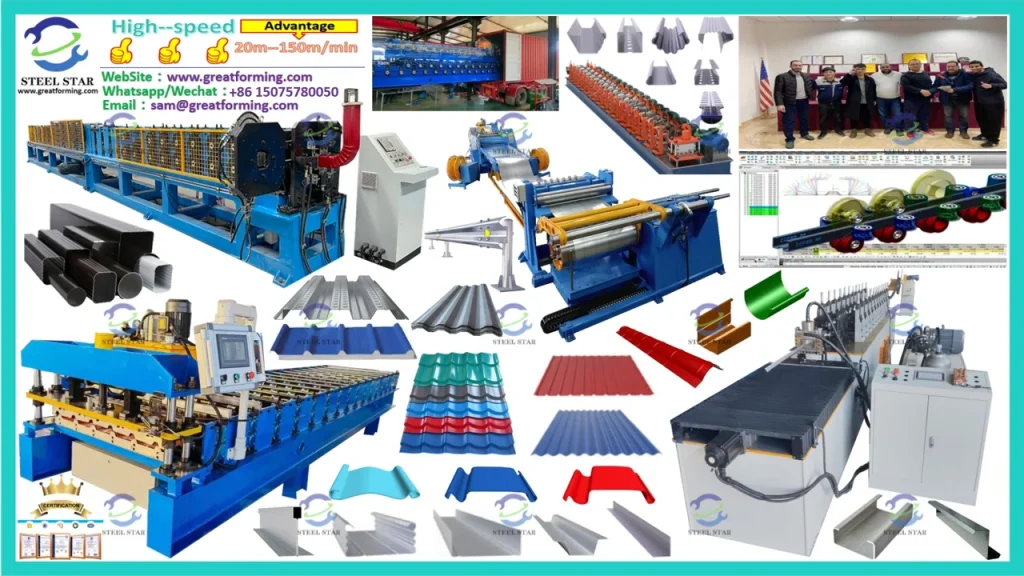