Steel Deck and Steel Deck Machine:
Introduction
In the construction and manufacturing industries, steel decks have become an essential component, and the machines that produce them play a crucial role in ensuring efficiency and quality. Steel decks offer numerous advantages, from structural support to versatility in design, while steel deck machines have evolved to meet the growing demands of modern construction projects.
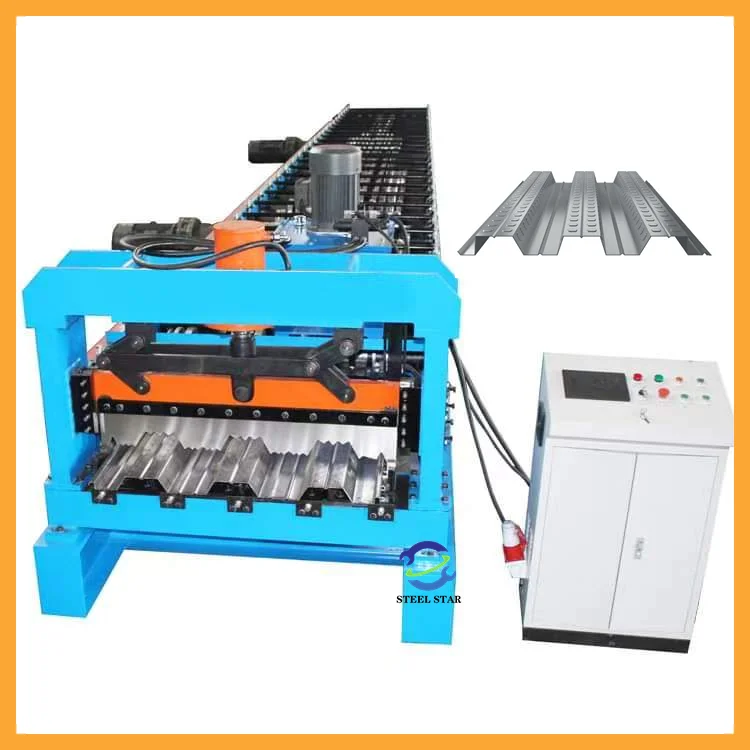
What is a Steel Deck?
A steel deck is a cold-formed, corrugated metal sheet that is primarily used in building construction. It serves multiple purposes. Structurally, it provides a platform for concrete slabs in composite floor systems. The corrugations enhance its strength-to-weight ratio, allowing it to span significant distances while supporting heavy loads. For example, in high-rise buildings, steel decks are laid down as a base on which concrete is poured, creating a composite structure that combines the tensile strength of the steel with the compressive strength of the concrete. This not only speeds up the construction process but also results in a more durable and stable floor system.
Functionally, steel decks can also act as permanent formwork, eliminating the need for traditional wooden formwork that requires removal after concrete curing. This saves time and labor costs. Moreover, they contribute to the fire resistance of the building. When properly designed and installed, the steel deck can help delay the spread of fire, providing crucial evacuation time.
Operation process and specifications
Start-up and parameter setting
Close the protective cover of the moving parts before starting, and set the forming line speed after the operation panel is powered on (normal 8-12m/min, pre-coated plate reduced to 5-8m/min).
Enter the length sizing parameters through the PLC system (±1mm accuracy requires servo control).
Rolling forming control
Feeding: Manual or automatic unwinder feeds at a uniform speed to ensure that the steel plate is aligned with the center line of the roller, and the offset is ≤2mm.
Forming monitoring: Observe the forming effect of the 3rd and 10th rollers, and adjust the pressing pressure in time (it is forbidden to exceed the equipment calibration value by 120%).
Shearing control: After the hydraulic shearing module is triggered, check the flatness of the cut (burr height ≤0.5mm is qualified).
Stop and reset
After completing production, press the emergency stop switch, the three-axis mechanism returns to the mechanical origin, turn off the main power supply and clean up the metal debris.
Key considerations
Safety regulations
Operators must wear cut-resistant gloves and goggles, and are strictly prohibited from touching the moving rollers or chains.
Insulated tools must be used to operate electronic switches in humid environments to avoid short circuit risks.
Fault response
Roller jam: Immediately stop the machine and jog in the reverse direction to release the pressure, and check whether there is any foreign matter entering the forming area.
Sizing deviation: Calibrate the photoelectric sensor or servo encoder, and review the PLC program logic.
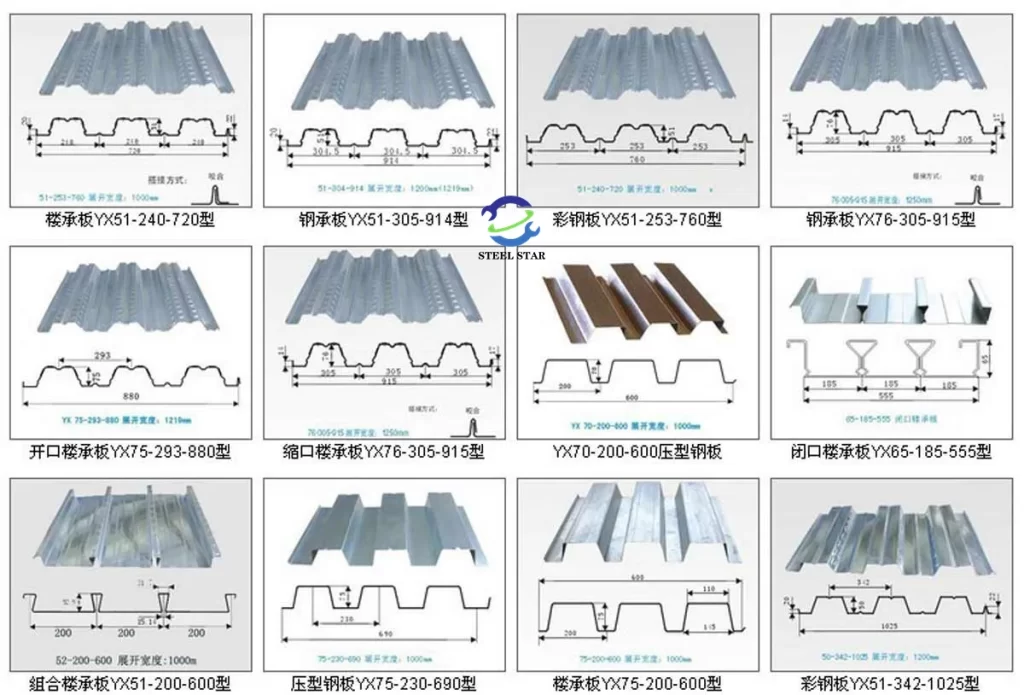
Steel Deck Machine: The Production Powerhouse
A steel deck machine is a complex piece of equipment that transforms flat steel coils into the corrugated steel decks. These machines operate on the principle of cold roll forming. The process begins with a decoiler that unwinds the steel coil. The flat steel strip then passes through a series of rollers, each set of rollers gradually forming the desired corrugation pattern. The rollers are carefully designed and adjusted to achieve precise dimensions and profiles.
Modern steel deck machines are highly automated. They are equipped with computer numerical control (CNC) systems that allow for quick changeovers between different deck profiles. This flexibility is vital as construction projects often demand a variety of steel deck types. The machines also have in-line punching and shearing capabilities. Punching stations create holes for fasteners or other connections, while shearing units cut the formed steel decks to the required lengths. This integrated production process significantly reduces production time and waste, improving overall productivity.
Future Trends
The steel deck and steel deck machine industries are continuously evolving. With the growing emphasis on sustainable construction, there is a push towards developing more ener.

Website:
www.greatforming.com (English)
www.arabicgreatforming.com (عربي)
www.russiangreatforming.com(Русский)
www.spanishgreatforming.com(Español)
www.frenchgreatforming.com(Français)
www.portuguesegreatforming.com(Portuguese)
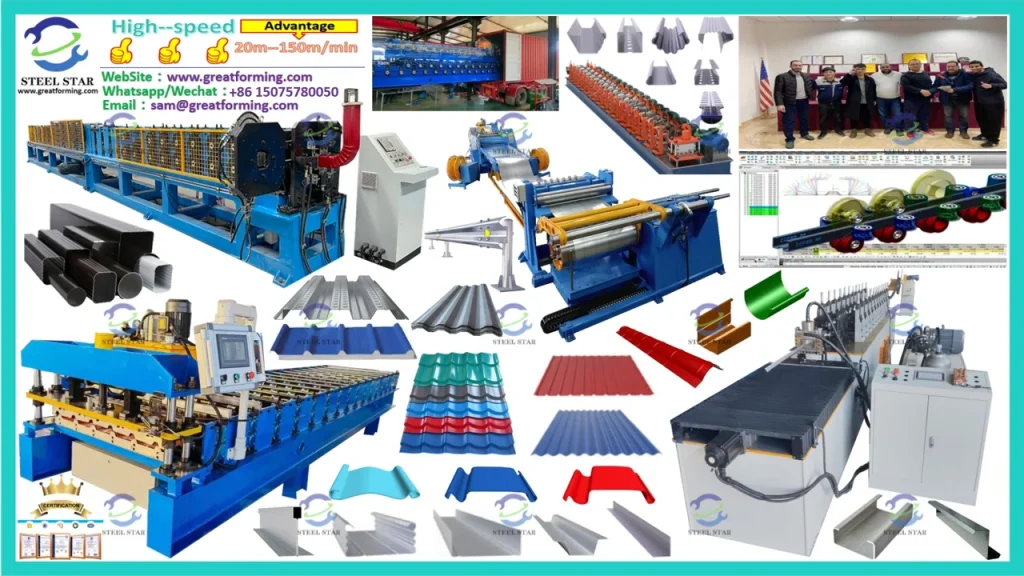