Guardrail Plate Roll Forming Machine: Revolutionizing Road Safety Infrastructure Production.
In the realm of modern transportation infrastructure, guardrails play a pivotal role in safeguarding lives and property by providing a crucial barrier along highways, bridges, and various roadways. Central to the efficient and precise manufacturing of these life-saving guardrail plates is the remarkable Guardrail Plate Roll Forming Machine, a technological marvel that has transformed the industry.
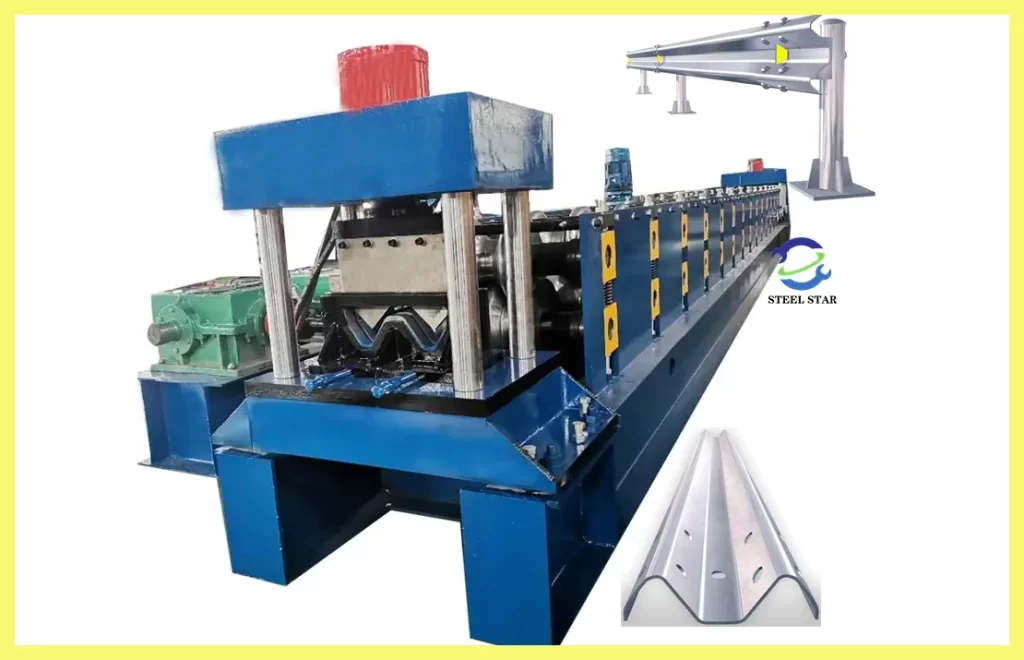
I. Operational Mechanics
The Guardrail Plate Roll Forming Machine operates on a meticulously designed sequence of processes. It all commences with the loading of a coil of raw material, typically high-strength steel, onto the decoiler unit. This decoiler, equipped with advanced tension control mechanisms, ensures a steady and uniform feed of the steel strip into the heart of the machine. As the strip progresses, it encounters a series of precisely engineered forming rollers.
These rollers, crafted from hardened alloy steel to withstand the rigors of continuous operation, are the artisans that sculpt the flat steel into the desired guardrail plate profile. Each roller has a specific function, with the initial ones imparting gentle bends and curvatures, gradually shaping the material. As the steel traverses further through the machine, subsequent rollers refine and perfect the shape, creating the characteristic wavy or corrugated pattern seen on guardrail plates. The rollers work in harmony, applying consistent pressure and guiding the material with micron-level precision, ensuring that every inch of the plate adheres to exacting dimensional standards.
Once the forming process is complete, the continuous length of guardrail plate reaches the cutting mechanism. This component, often driven by servo motors for unerring accuracy, slices the plate into predetermined lengths. Advanced control systems allow operators to input the desired length specifications, and the machine executes the cuts with remarkable speed and precision, readying the individual guardrail plates for further processing or installation.
II. Key Components and Their Significance
- Decoiler: As mentioned, the decoiler is the gatekeeper of the raw material supply. Its tension control system is not just a convenience but a necessity. By maintaining the correct tension, it prevents issues like material wrinkling or stretching. In a busy manufacturing facility churning out guardrail plates for a major highway project, any deviation in tension could lead to defective plates, causing costly delays and rework.
- Forming Rollers: These are the stars of the show. Their custom-designed profiles are based on extensive engineering research and comply with industry standards for guardrail strength and impact resistance. For instance, the specific wave height and pitch of the corrugations are calculated to absorb and dissipate the force of a vehicle impact effectively. Replaceable inserts on the rollers also allow for quick modifications to produce different guardrail plate variants, catering to diverse project requirements.
- Cutting Device: The precision of the cutting device is what transforms the continuous roll-formed plate into manageable, standardized lengths. In applications where guardrails need to be installed in sections with seamless joints, the accurate cutting ensures a perfect fit. This is especially critical in bridge installations, where even a millimeter of error could disrupt the integrity of the entire guardrail system.
- Control Panel: The nerve center of the machine, the control panel, offers operators a user-friendly interface to oversee and adjust all parameters. From roller speeds to forming pressures and cutting lengths, every aspect of the production process can be fine-tuned. This adaptability is invaluable, as it enables the machine to switch between different production runs for various guardrail designs or project specifications with minimal downtime.
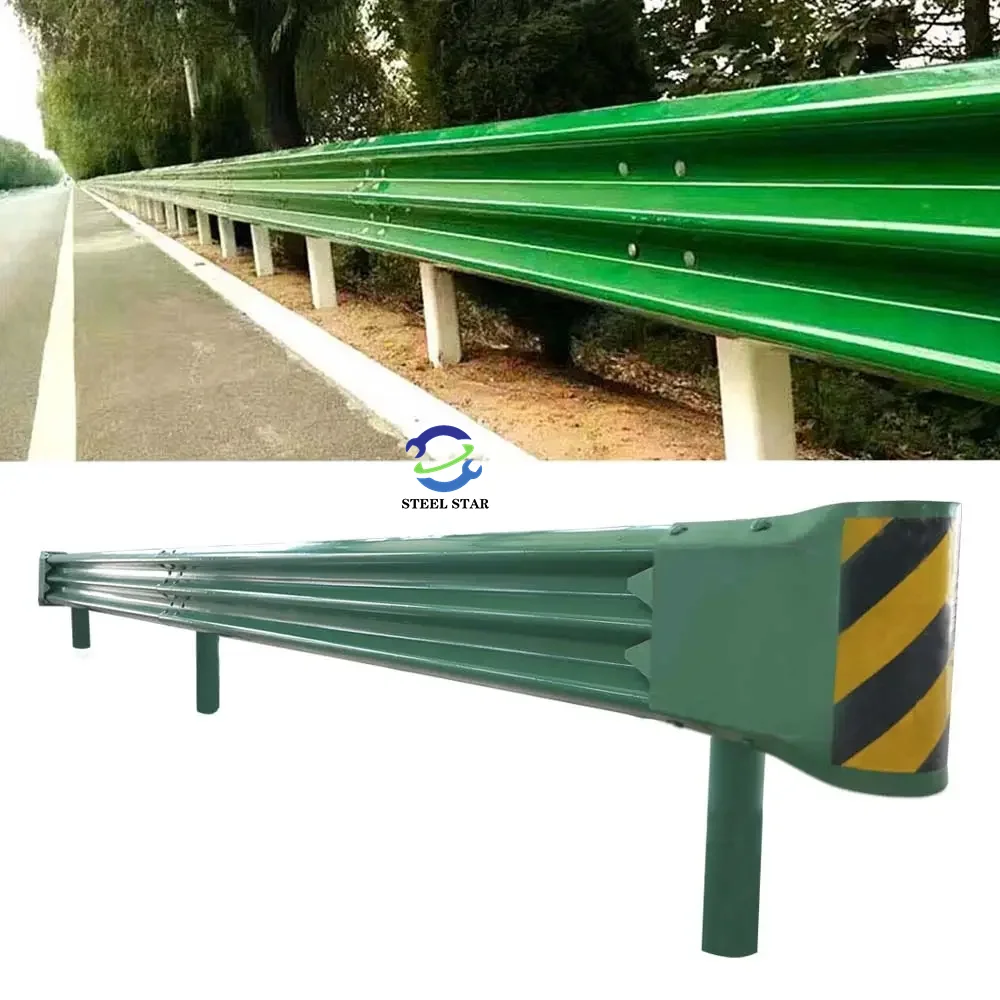
III. Advantages in Guardrail Production
- Enhanced Efficiency: Traditional methods of fabricating guardrail plates, involving manual cutting and shaping, were labor-intensive and time-consuming. The roll forming machine has revolutionized this. It can produce guardrail plates at a rate that far surpasses manual production, sometimes generating dozens of finished plates per minute. This rapid output is a boon for large infrastructure projects with tight deadlines, such as the construction of a new interstate highway, where thousands of linear feet of guardrails are needed.
- Cost Savings: By automating the process, labor costs are significantly reduced. Fewer workers are required to oversee the production line, freeing up human resources for other essential tasks. Additionally, the precise material usage due to the machine’s accuracy minimizes waste. In a cost-conscious industry, where steel prices can fluctuate, optimizing material consumption can translate into substantial savings over the course of a large production run.
- Superior Quality and Consistency: Every guardrail plate emerging from the roll forming machine is a clone of its predecessors in terms of quality and dimensions. This uniformity is crucial for ensuring the structural integrity of the guardrail system. When installed, these consistent plates provide a seamless and reliable barrier. In contrast, handcrafted plates were prone to variations that could compromise the overall performance of the guardrail, especially during a collision event.
IV. Applications and Industry Impact
Guardrail plates manufactured by these machines find ubiquitous use in the transportation sector. On highways, they form the first line of defense against errant vehicles, preventing them from veering off the road and into dangerous terrain or oncoming traffic. In urban areas, they protect pedestrians and cyclists along busy streets and bridges. For instance, in a bustling city center with a complex network of overpasses and elevated roads, the precisely fabricated guardrail plates offer peace of mind to both motorists and those on foot.
Moreover, the impact of these machines extends beyond immediate production. They have spurred innovation in guardrail design, as manufacturers can now experiment with new materials and profiles more easily. With the ability to quickly adjust the roll forming process, research and development efforts have led to the creation of guardrails with enhanced energy-absorption capabilities, better corrosion resistance, and improved aesthetics, all while maintaining the highest safety standards.
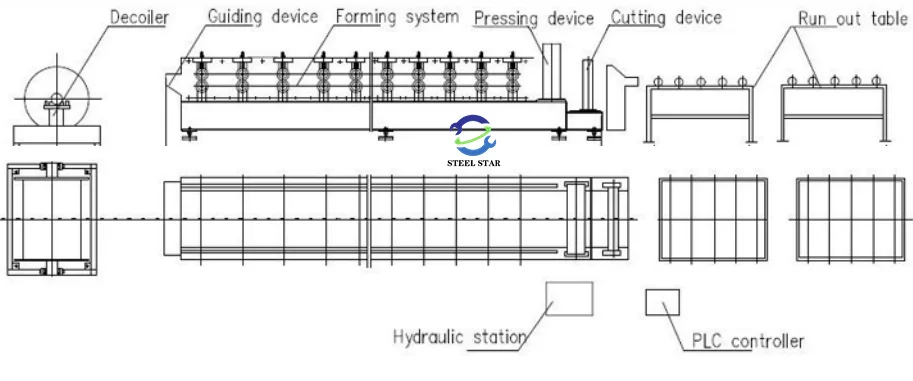
V. Future Prospects
As technology hurtles forward, the Guardrail Plate Roll Forming Machine is poised for further evolution. The integration of artificial intelligence and machine learning algorithms is on the horizon. These intelligent systems could predict maintenance needs, optimize production parameters in real-time based on raw material quality fluctuations, and even detect potential defects during the forming process before they become major issues.
Furthermore, with a growing emphasis on sustainable infrastructure, there is a push towards using recycled or more environmentally friendly materials. The roll forming machines of the future will likely be adapted to handle these novel materials, opening the door to greener guardrail solutions that still provide uncompromising safety. In conclusion, the Guardrail Plate Roll Forming Machine has not only streamlined guardrail production but also holds the key to a safer, more efficient, and sustainable future for our roads and transportation networks.
Website:
www.greatforming.com (English)
www.arabicgreatforming.com (عربي)
www.russiangreatforming.com(Русский)
www.spanishgreatforming.com(Español)
www.frenchgreatforming.com(Français)
www.portuguesegreatforming.com(Portuguese)
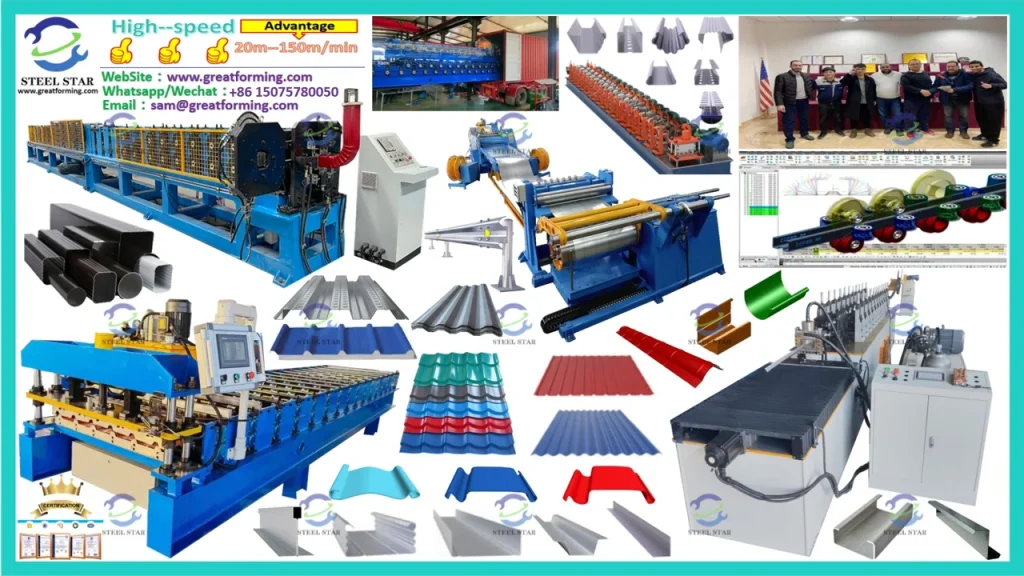