Metal Roll Machines, Forming Machines, and Roll Forming Machines are essential types of equipment used in the metalworking industry for shaping metal into various continuous profiles and panels. Here’s an overview of their purpose, working principles, and common applications:
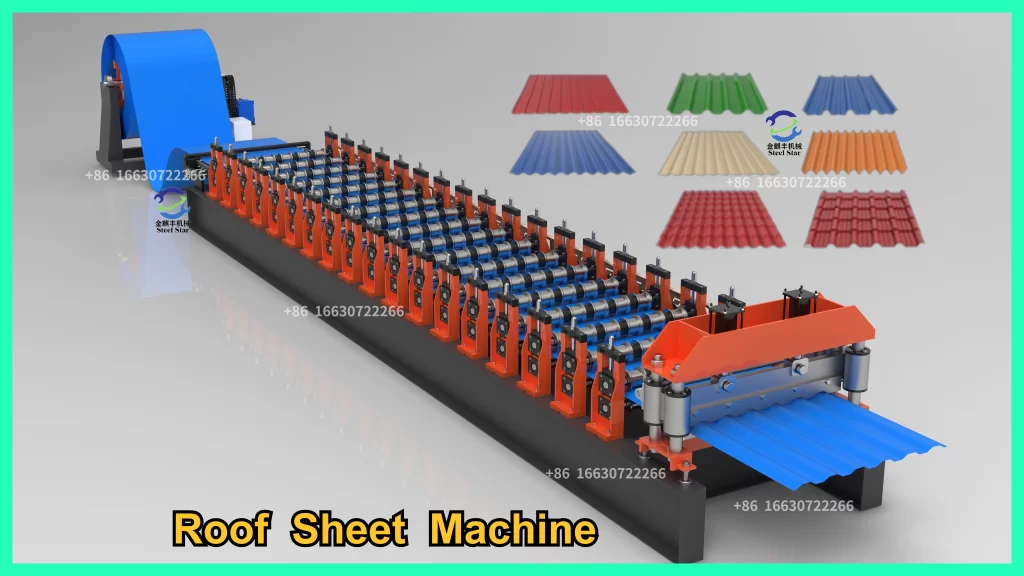
We use the most advanced roll forming design software COPRA
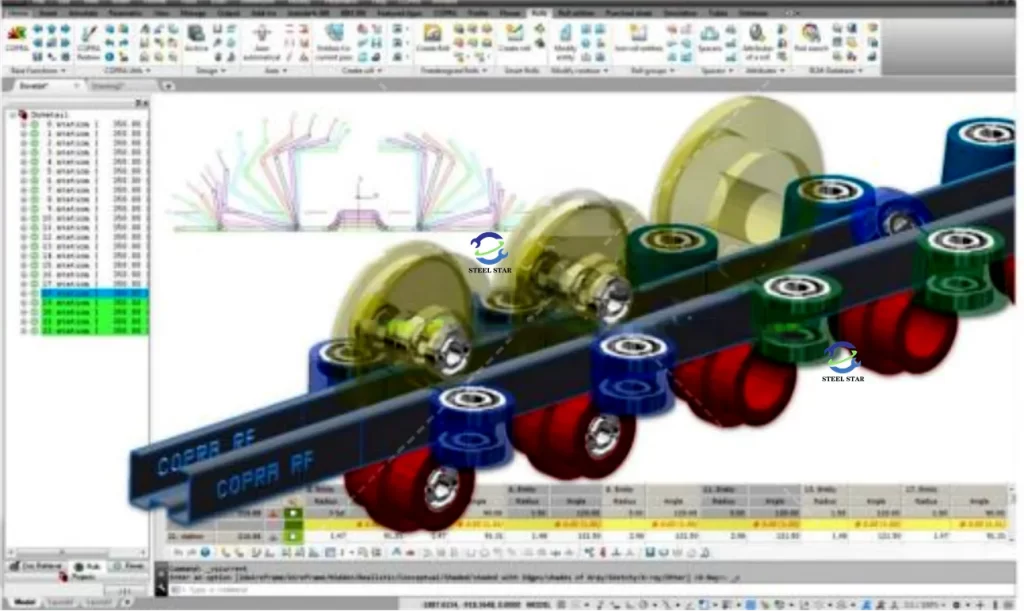
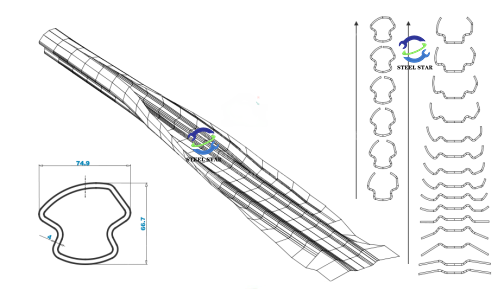
1. What is a Roll Forming Machine?
A roll forming machine is a type of machine used to shape long strips of metal (typically coiled steel) into specific cross-sectional profiles. The process involves gradually bending the metal as it passes through a series of sequential rollers, each set designed to perform incremental changes until the desired shape is achieved.
2. Key Components of Roll Forming Machines:
- Decoiler/Uncoiler: Holds and unwinds the metal coil for feeding into the machine.
- Rollers/Stations: A series of precisely aligned rollers that progressively bend the metal strip to create the profile.
- Cutting System: Typically a hydraulic or mechanical cutting tool that trims the metal to the required length after forming.
- Control System: Often equipped with a PLC (Programmable Logic Controller) for automated operation, allowing precise control over speed, length, and batch settings.
- Output Conveyor/Table: Where the completed metal sections are placed after cutting.
3. Types of Roll Forming Machines:
- Single Profile Machines: Designed to produce one type of profile, such as a specific panel or channel.
- Multi-Profile Machines: Can be adjusted to produce different shapes by changing the roller configuration.
- Portable Roll Forming Machines: Smaller machines that can be transported to job sites for on-location panel production.
- Custom Roll Formers: Tailored to meet specific production needs for unique or specialized profiles.
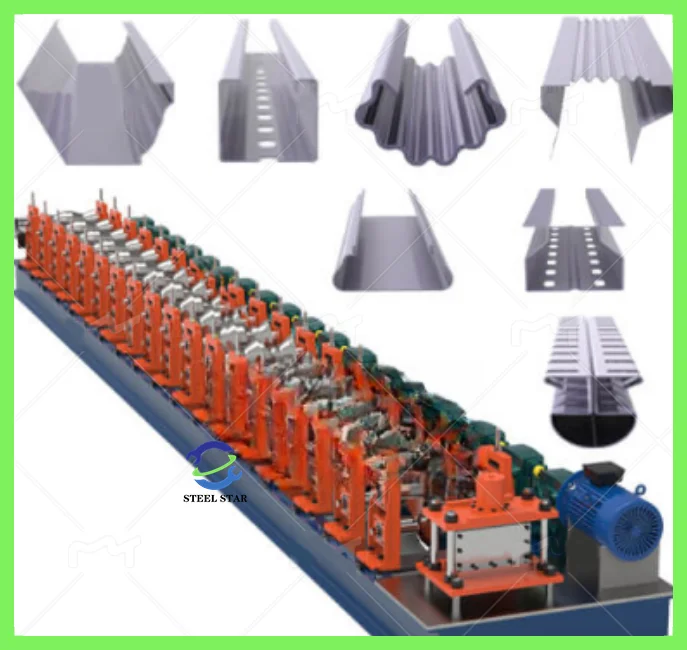
4. Applications of Roll Forming Machines:
- Roofing Panels: Production of metal roof sheets like standing seam panels, corrugated sheets, and trapezoidal panels.
- Structural Components: Manufacturing beams, channels, and framing for construction.
- Automotive Industry: Creating components like door frames, reinforcements, and trim.
- Furniture and Appliances: Producing parts for desks, shelving, and other metal furniture.
- HVAC Ducting: Fabrication of ducts and pipes for ventilation systems.
5. Advantages of Roll Forming:
- High Production Speed: Efficiently produces long lengths of metal components with minimal waste.
- Consistency and Precision: Ensures that all products have consistent shapes and dimensions.
- Reduced Material Handling: The continuous feed and automated operation reduce the need for manual intervention.
- Customization Options: Allows for custom shapes and profiles to be created according to specific design requirements.
- Low Operational Cost: Energy-efficient and minimal labor requirement due to automation.
6. Working Process of a Roll Forming Machine:
- Loading: A metal coil is loaded onto the decoiler.
- Feeding: The metal strip is fed into the forming rollers.
- Forming: As the strip moves through the rollers, each set bends it incrementally until the desired profile is complete.
- Cutting: The shaped metal is cut to the required length using the cutting mechanism.
- Output: Finished parts are deposited on the output table or conveyor.
7. Materials Used:
- Steel (Galvanized, Stainless, etc.)
- Aluminum
- Copper
- Other alloys as needed for specific applications.
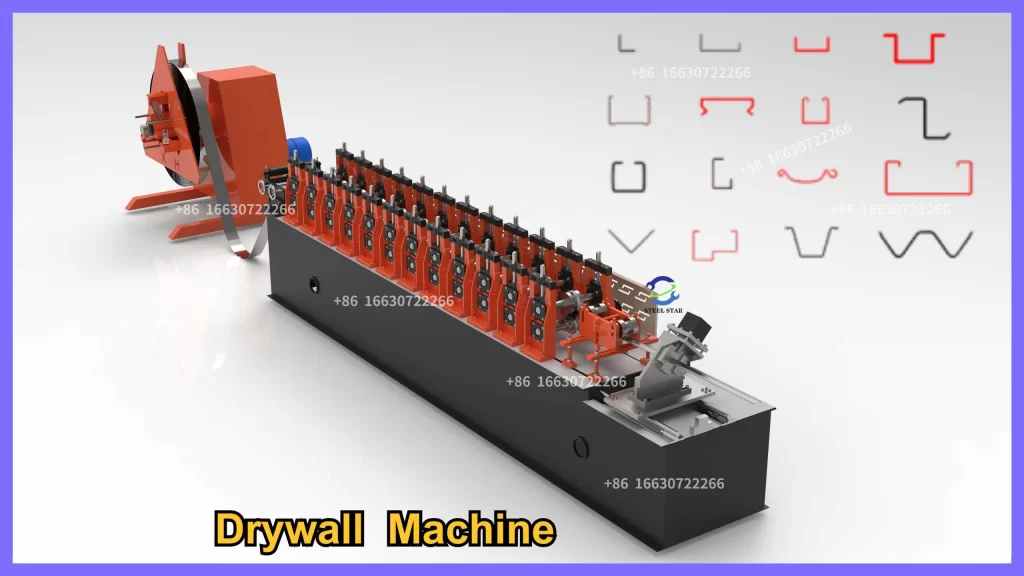
Roll forming machines are highly valuable in industries where continuous, high-precision production of metal profiles is required, providing versatility and efficiency for large-scale manufacturing.
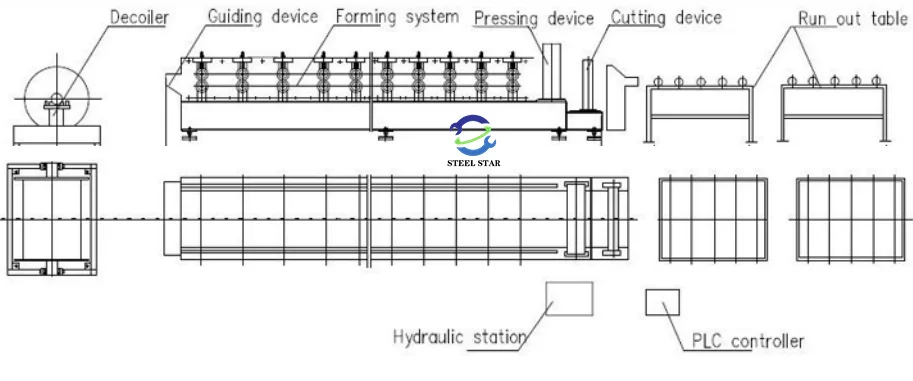
Website:
www.greatforming.com (English)
www.arabicgreatforming.com (عربي)
www.russiangreatforming.com(Русский)
www.spanishgreatforming.com(Español)
www.frenchgreatforming.com(Français)
www.portuguesegreatforming.com(Portuguese)
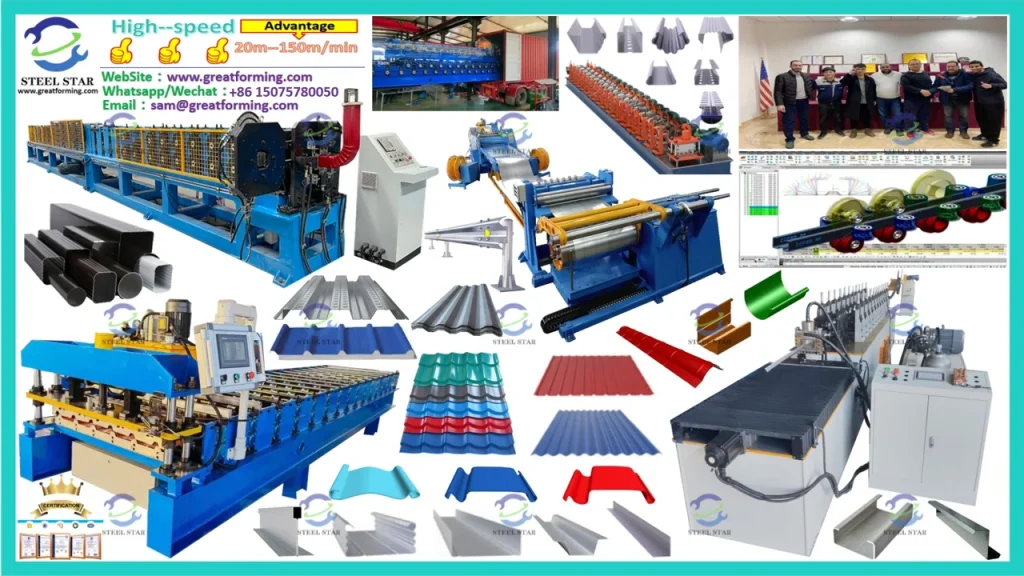