Roof Panel Machines, Roof Sheet Machines, and Roof Roll Forming Machines are types of roll forming equipment specifically designed to produce various types of metal roofing panels and sheets used in the construction industry. Here’s an overview of their functions, features, and common applications:
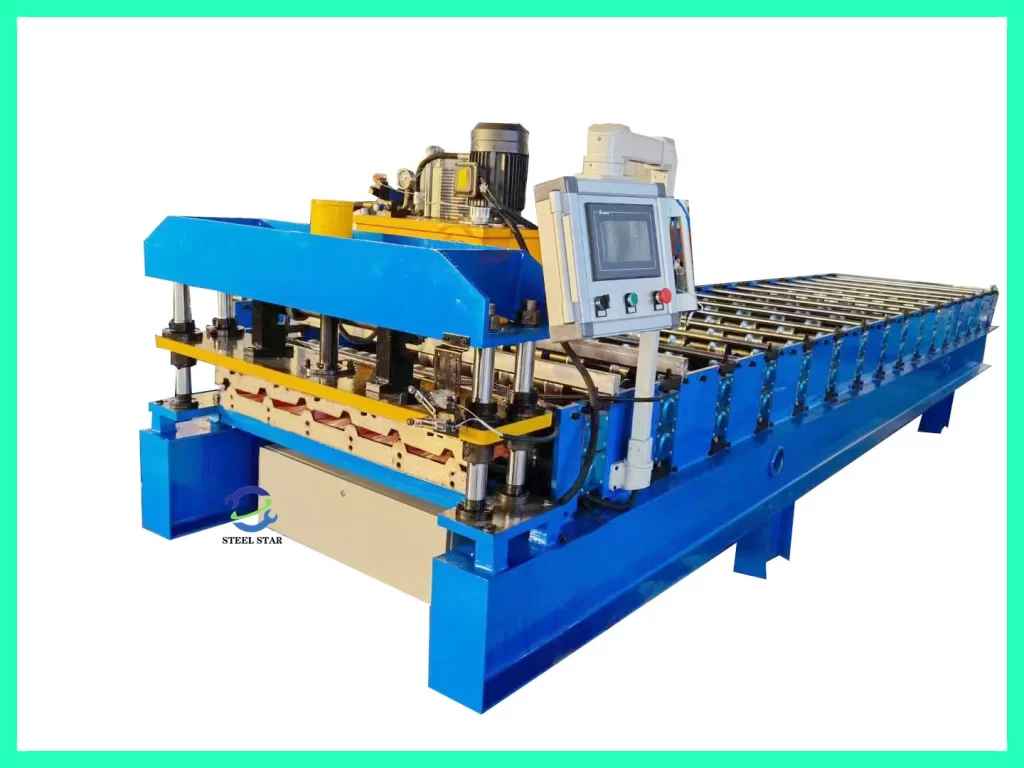
1. Overview and Purpose:
These machines are engineered to transform flat metal coils into roof panels with specific profiles and lengths, ensuring high precision and efficiency. They are essential for manufacturing roofing materials that are durable, weather-resistant, and tailored to fit construction requirements.
2. Key Features of Roof Panel Machines:
- Decoiler/Uncoiler: Holds the metal coil and unwinds it for feeding into the roll forming machine.
- Roll Forming System: Composed of a series of rollers that shape the metal gradually to form specific roofing profiles.
- Cut-to-Length System: A hydraulic or pneumatic cutting mechanism ensures panels are trimmed to the desired length without affecting the profile.
- Control Panel: PLC or computerized control for setting production parameters like panel length, width, and batch quantity.
- Output Conveyor/Table: Where finished panels are placed after being cut.
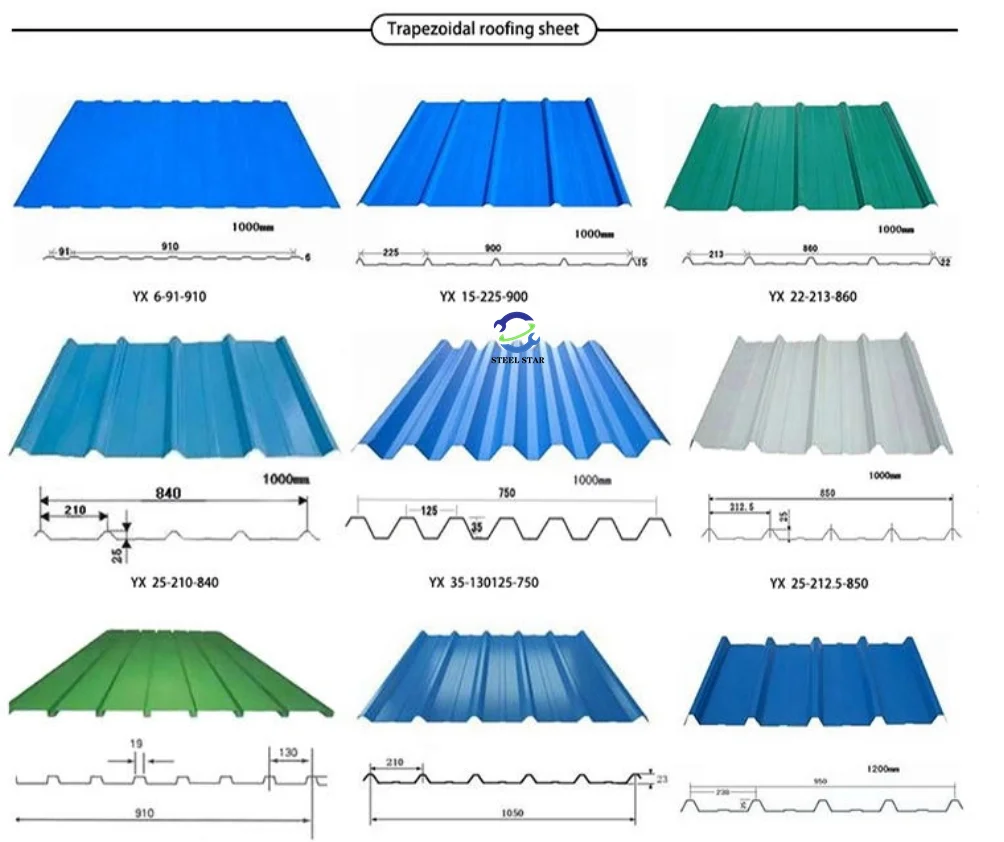
3. Types of Roofing Profiles Produced:
- Standing Seam Panels: Popular for modern and commercial buildings, known for their sleek appearance and strong weather resistance.
- Corrugated Sheets: Characterized by wavy designs that offer structural integrity and a traditional look, often used in both residential and industrial structures.
- Trapezoidal Panels: Feature angled shapes that provide excellent load-bearing capacity.
- Tile Profile Sheets: Resemble traditional roof tiles but are made of metal, offering a combination of aesthetic appeal and durability.
4. Advantages of Roof Roll Forming Machines:
- High Efficiency: Continuous production allows for quick output of large quantities of roofing panels.
- Customization: Machines can be set up to produce panels in various profiles, thicknesses, and lengths.
- Precision: Advanced control systems ensure uniformity and accuracy in every panel.
- Durability: The formed panels are strong, long-lasting, and can withstand harsh environmental conditions.
- Cost-Effective: Reduces labor costs and minimizes material waste through automated operation.
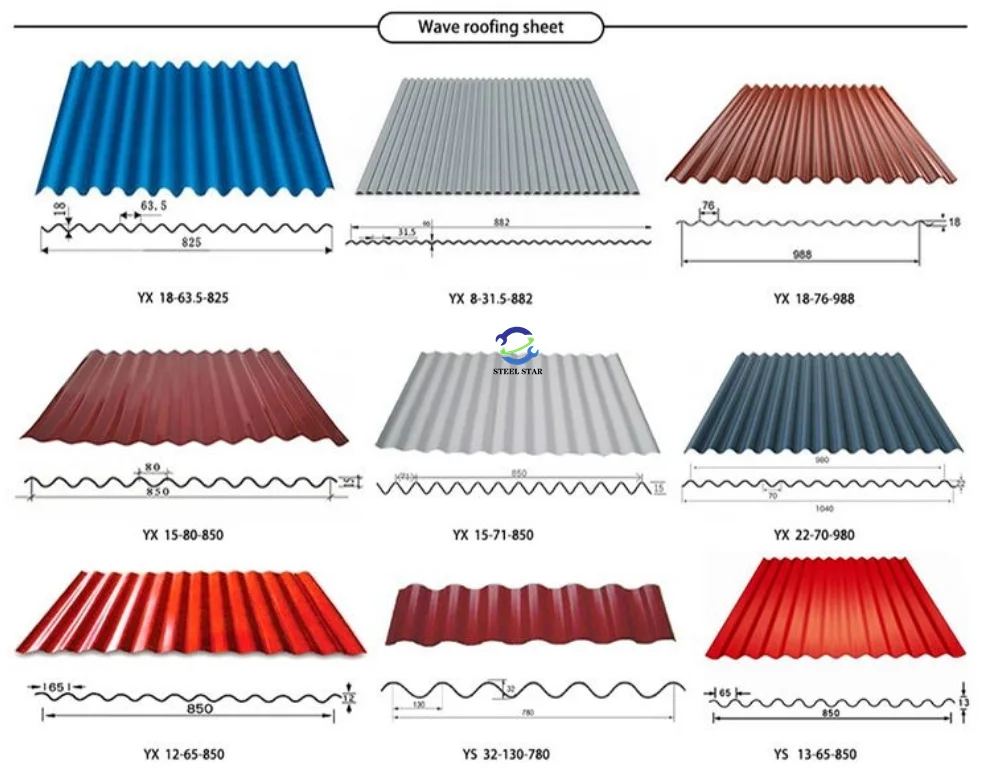
5. Applications:
- Commercial Roofing: Warehouses, factories, shopping centers, and office buildings.
- Residential Roofing: Houses, apartment complexes, and residential extensions.
- Agricultural Structures: Barns, silos, and storage sheds.
- Industrial Facilities: Production plants and workshops.
6. Customization Options:
- Embossing Features: To add texture or decorative elements to the panels.
- Insulation Capability: Machines can be configured to produce insulated panels for better thermal efficiency.
- Color Coating Integration: Some machines can work with pre-painted coils to create panels with a finished, colored surface.
- Portable Machines: Compact and portable roll forming machines are available for on-site production, ideal for contractors.
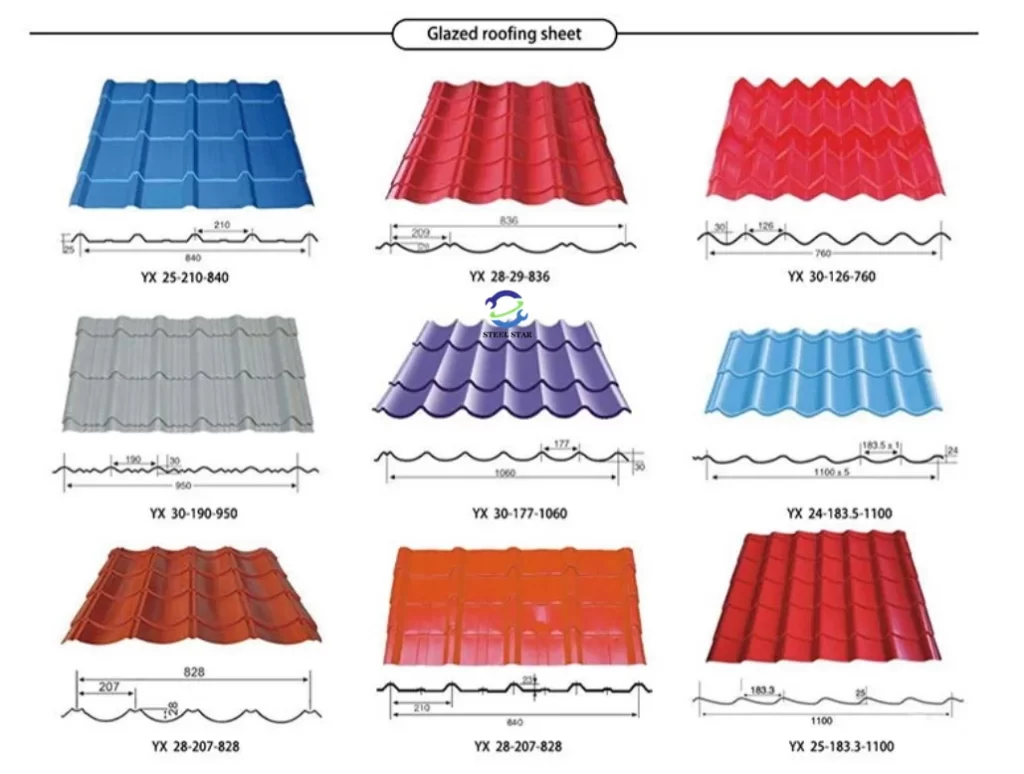
7. Buying Tips:
- Check for Support and Maintenance: Ensure the manufacturer offers training, spare parts, and technical support.
- Customization Needs: Assess whether you need specific features or profiles for your projects.
- Quality Assurance: Look for machines that come with warranties and certifications, such as ISO, to guarantee high standards.
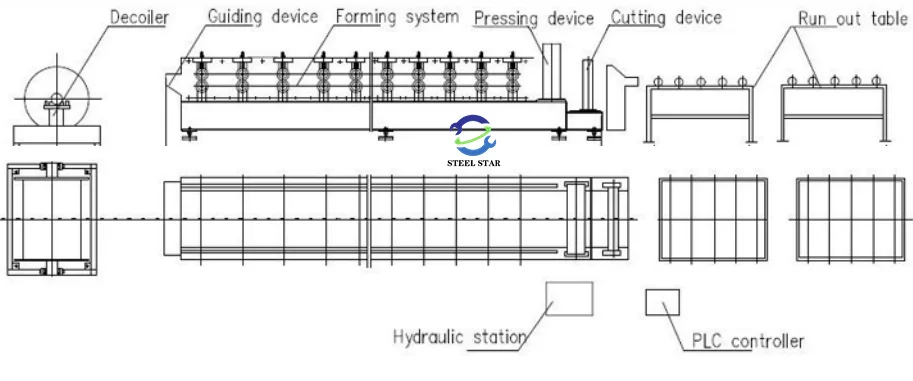
Roof panel and sheet machines are essential tools for the roofing industry, providing reliable solutions for creating high-quality, customized roofing materials that meet specific structural and aesthetic needs.
Website:
www.greatforming.com (English)
www.arabicgreatforming.com (عربي)
www.russiangreatforming.com(Русский)
www.spanishgreatforming.com(Español)
www.frenchgreatforming.com(Français)
www.portuguesegreatforming.com(Portuguese)
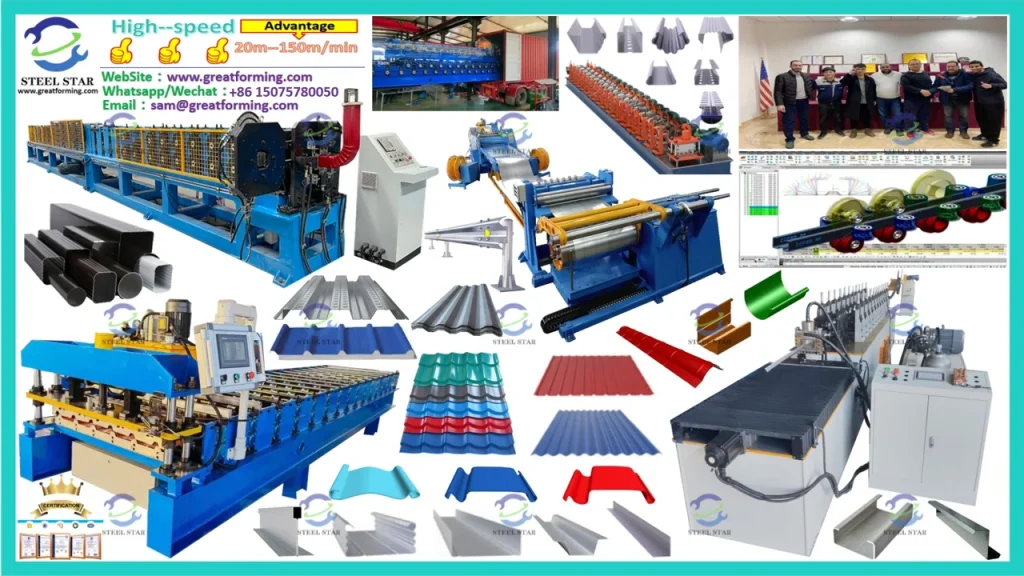