Roofing Sheet Machines: A Cornerstone of the Construction Industry.
I. Introduction
In the ever – evolving landscape of construction, roofing sheet machines stand as crucial assets. These machines are the backbone of the production process for roofing sheets, which are essential for protecting buildings from the elements. From residential houses to large – scale industrial complexes, the quality and efficiency of roofing sheet production hinge on the performance of these specialized machines.
II. Types of Roofing Sheet Machines
A. Roll – Forming Machines
Function and Process
Roll – forming machines are among the most common types of roofing sheet machines. They operate by passing a continuous strip of metal, such as steel or aluminum, through a series of rollers. These rollers gradually shape the metal into the desired profile, whether it’s a corrugated pattern for enhanced strength and water runoff in industrial roofing or a more complex profile for aesthetic and functional purposes in residential applications. The process is highly automated, allowing for high – speed production with consistent quality.
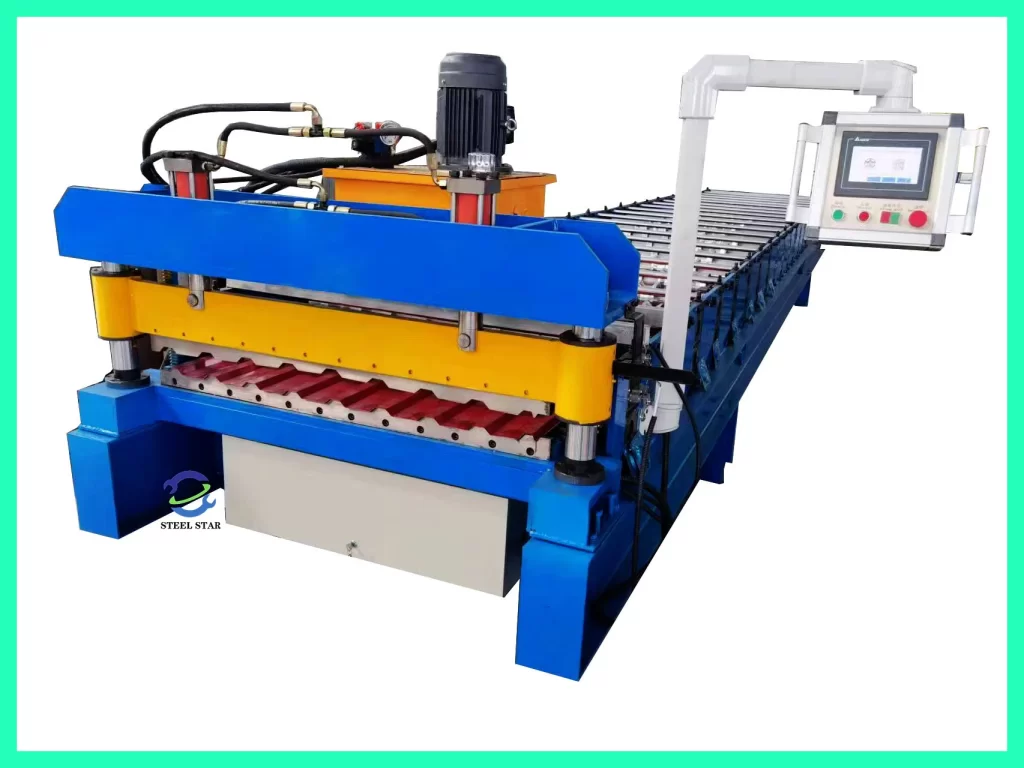
Advantages
Precision: Roll – forming machines can achieve extremely precise dimensions, ensuring that each roofing sheet produced fits perfectly during installation. This precision reduces waste and simplifies the construction process.
Versatility: They can be adjusted to produce a wide variety of roofing sheet profiles, making them suitable for different architectural designs and construction requirements. For example, by changing the roller sets, the machine can switch from producing standard corrugated sheets to trapezoidal or sinusoidal profiles.
Advantages
Material Adaptability: Extrusion machines can work with a range of non – metal materials, each offering unique properties such as transparency (in the case of polycarbonate for applications like greenhouses) or flexibility (in some PVC – based roofing sheets).
High – Volume Production: They are capable of producing large quantities of roofing sheets in a relatively short time, meeting the demands of large – scale construction projects.
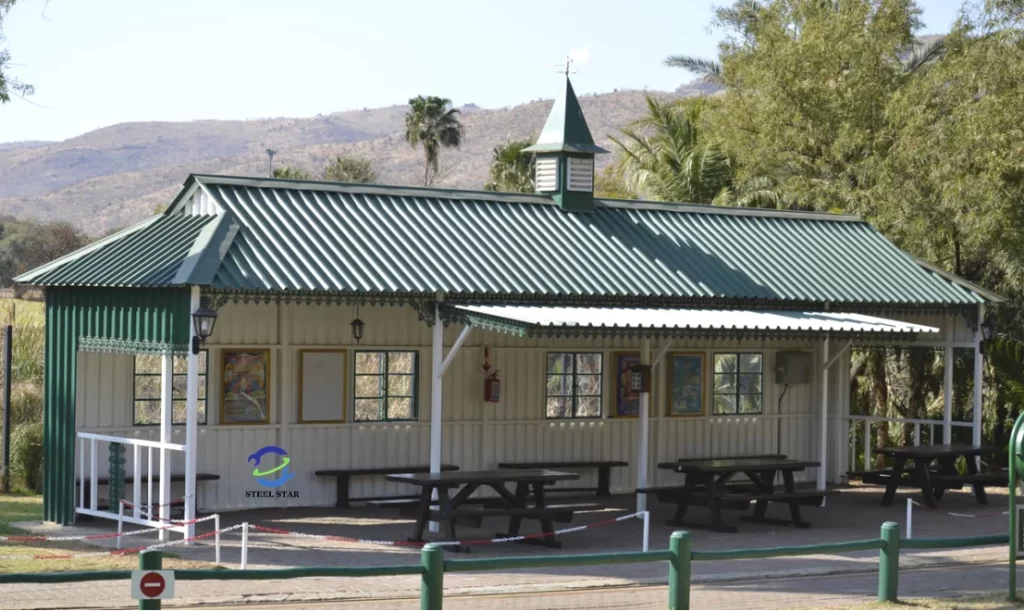
III. Key Components of Roofing Sheet Machines
A. Feeding Systems
Function
The feeding system is responsible for delivering the raw material, whether it’s a metal coil or plastic pellets, to the main processing unit of the machine. In the case of roll – forming machines for metal sheets, the coil feeding system must ensure a smooth and continuous supply of metal, maintaining a consistent tension to prevent wrinkles or jams during the rolling process. For extrusion machines, the feeding system accurately measures and conveys the plastic pellets to the hopper, where they are then fed into the extruder barrel.
Importance
A well – designed feeding system is essential for the overall performance of the roofing sheet machine. It directly impacts the quality of the final product. If the feeding is inconsistent, it can lead to variations in the thickness or shape of the roofing sheet, resulting in defective products.
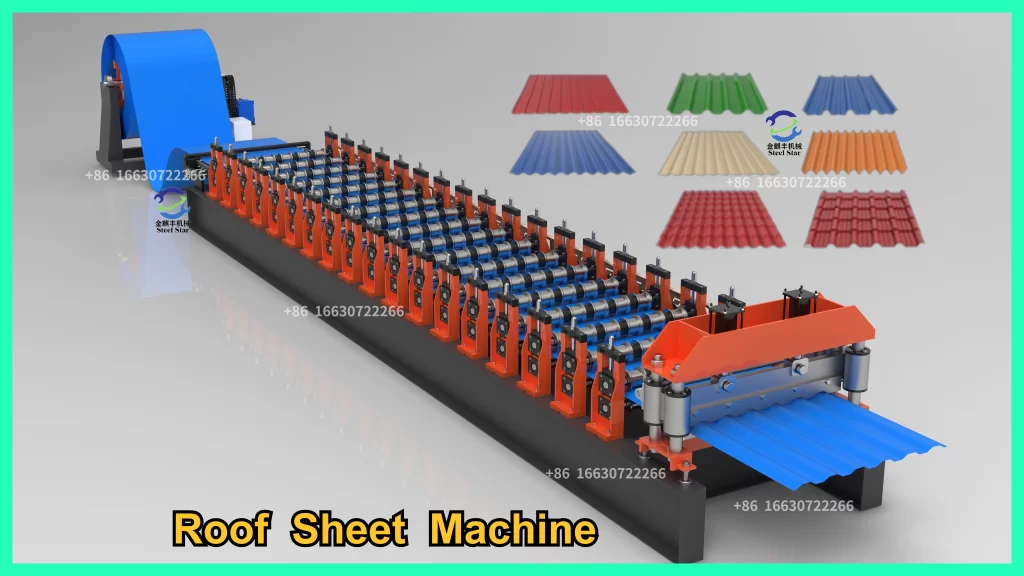
B. Shaping and Molding Units
Function
This is the heart of the roofing sheet machine. In roll – forming machines, the shaping unit consists of multiple sets of rollers arranged in a specific sequence. Each set of rollers gradually deforms the metal strip into the desired profile. In extrusion machines, the die is the key component of the molding unit. It determines the cross – sectional shape of the roofing sheet, and its design is crucial for achieving the correct dimensions and surface finish.
Importance
The accuracy and precision of the shaping and molding units are directly related to the quality and functionality of the roofing sheets. A well – maintained and properly designed shaping unit ensures that the roofing sheets have the right shape for effective water drainage, structural integrity, and aesthetic appeal.
Website:
www.greatforming.com (English)
www.arabicgreatforming.com (عربي)
www.russiangreatforming.com(Русский)
www.spanishgreatforming.com(Español)
www.frenchgreatforming.com(Français)
www.portuguesegreatforming.com(Portuguese)
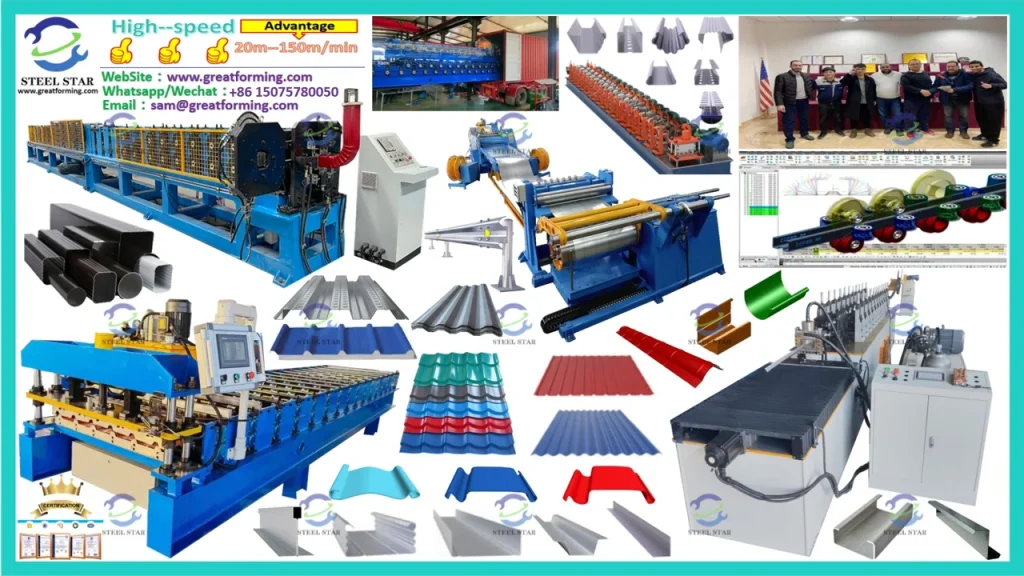